Influence of Gripping Moments during Wheelchair Propulsion on Natural Surfaces
Hongwu Wang, Alicia M. Koontz, Jennifer L. Collinger, Michael L. Boninger
Dept. of Rehab. Science and Technology, University of Pittsburgh, Pittsburgh, PA 15260
Human Engineering Research Laboratories, Highland Drive VA Medical Center, Pittsburgh, PA
ABSTRACT:
This study investigated gripping moments during propulsion of experienced manual wheelchair users and compared the moments between two commonly traversed level surfaces (linoleum and carpet) and a ramp. Twenty-three manual wheelchair users (MWUs) who took part in the 2005 National Veterans Wheelchair Games in Minneapolis, MN at the Minneapolis Convention Center propelled their wheelchairs from rest to a comfortable pace on each surface while kinetic and kinematic data were collected. Reliable and valid instruments including the SmartWheelsTM (Three Rivers Holdings, Mesa, AZ) and a six camera Vicon MXmotion camera system (Vicon, Lake Forest, CA) were used for data collection. Peak and average gripping moment as well as peak and average hub moment, average velocity of propulsion were calculated for the first three strokes of each propulsion trial. A two-way repeated measures analysis of variance (ANOVA) with factors stroke number and surface followed by a Bonferroni adjustment post test were used for data analysis. The α value was set at 0.05. The average gripping moments (absolute value, no consideration of direction) were 2.81+1.47 (N*m), 3.02+1.18 (N*m) and 2.43+0.99 (N*m) which comprised 16.87 + 7.43 %, 20.17 + 12.65 % and 20.04 + 7.62 % of the average moments measured at the hub for carpet (16.02+4.35 N*m), ramp (17.47+4.93 N*m) and the linoleum (13.08+4.00) surface, respectively. The magnitude of the grip moments for both ramp and carpet were significantly higher than for linoleum. On each surface, more positive than negative gripping moments were generated which may have assisted the MWUs in delivering more effective forces to the pushrim. The relative contribution of gripping moments to the total moment measured at the hub was comparable between the linoleum and ramp surfaces which may be an indication that more grip force is being used on linoleum than is necessary thereby contributing to inefficiencies in propulsion technique and possibly increasing the risk of developing wrist pain or CTS. Investigating gripping moments on an individual basis may help to identify opportunities for intervention or to identify those who may be a greater risk for developing CTS due to poor propulsion technique.
KEYWORDS:
spinal cord injury, biomechanics, mobility, kinetics, manual wheelchair
BACKGROUND:
Manual wheelchair users’ hands are capable of grasping the pushrim and creating moments about the wheelchair hub during wheelchair propulsion. These moments are referred to as ‘gripping moments’ in this paper. During wheelchair propulsion, the moment data measured around the hub of an instrumented wheel includes the gripping moment in addition to the moment acting at the center of pressure. Thus, an estimate of gripping moment can be determined by subtracting the applied moments acting at the center of pressure from moment data measured at the hub. Veeger et al [1] reported that the gripping moments were 5 N*m, which contributed approximately 31% of the moments measured at the hub, whereas Vansickle et al [2] reported that gripping moments were less than 1 N*m in any direction and were thus negligible. In Yang et al [3] gripping moments were estimated to be 14% and 11% of the propulsion moments measured at the hub during slow and fast speeds, respectively. In addition they showed that these moments were not negligible as they can affect the accuracy of tangential force and mechanical effective force calculations. All the prior studies of gripping moment were conducted using some form of stationary wheelchair propulsion or simulator. In addition to this, the conflicting results concerning the magnitudes of gripping moments shown in previous studies led us to investigate gripping moments during propulsion over real surfaces.
The purpose of this study was to quantify gripping moments during propulsion of experienced manual wheelchair users and compare the moments between two commonly traversed level surfaces (linoleum and carpet) and a ramp. Carpal tunnel syndrome is highly prevalent among manual wheelchair users [4] and is believed to be associated with repetitive forceful tasks and wrist flexor activity. As gripping moments are indicative of wrist musculature activity, quantifying their role during wheelchair propulsion over real surfaces might help explain the high prevalence of carpal tunnel syndrome (CTS) among manual wheelchair users (MWUs).
METHODS:
Subjects:
Thirty-one MWUs (30 men and 1 woman) were recruited in this study. The study took place at the Minneapolis Convention Center during the 2005 National Veterans Wheelchair Games in Minneapolis, MN and was approved by the VA National Special Events Committee, local Pittsburgh VA Research and Development Committee, VA Human Studies Subcommittee as well as the University of Pittsburgh’s Institutional Review Board. To be included in the study subjects had to 1) own a manual wheelchair and 2) have no history of upper limb fractures or dislocations that they had not recovered from. All research subjects signed an informed consent document before testing began.
Experiment protocol:
The wheelchairs were fitted bilaterally with SmartWheelsTM (Three Rivers Holdings, Mesa, AZ). Asato et al [5] demonstrated that the SmartWheel has excellent accuracy, linearity and precision. Force and torque sensing pushrims measured Fx, Fy, Fz, Mx, My and Mz for a six degree of freedom wheel in a global reference system. Reflective markers were placed on the left third metacarpalphalangeal joint (3MP), as well as the left rear axle of their wheelchair. A six camera Vicon MXmotion camera system (Vicon, Lake Forest, CA) was used to record at 60 Hz the position of the 3MP and rear axle of the subject’s manual wheelchair during propulsion. The six cameras were aligned next to each other and facing the left side of the wheelchair user. The surfaces tested included linoleum, high-pile carpet, and a plywood ramp with a five degree grade (maximum ADA compliant ramp grade of 1:12). Each was positioned in front of the cameras as the cameras remained stationary throughout the testing. The linoleum remnant was 1.20 m x 4.50 m (4’ by 15’), the carpet remnant was 1.50 m x 4.50 m (5’ by 15’) and the ramp was 1.2 m x 3.6 m (4’ by 12)’ with a 1.20 m x 1.20 m (4’ x 4’) platform landing at the top. A metal strip 1.2 m x 0.30 m (4’ by 1’) was placed at the bottom of the ramp to ease the transition from a level surface to an incline. Each surface was completed in a random order. Subjects started from rest at the far end of the remnant or in front of the metal strip at the bottom of the ramp and were instructed to push in a straight line up to a comfortable pace until they surpassed the end of the remnant or reached the landing platform. Three trials over each surface were recorded. SmartWheel data were collected at 240 Hz and afterwards, the kinetic data were linearly interpolated for synchonization with the kinematic data collection rate of 60 Hz.
Data analysis:
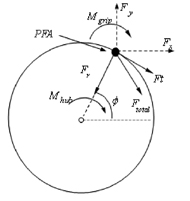
Although the hand can apply a moment about any of the three-dimensional coordinate axes, Sabick et al [6] showed that gripping moments in the frontal and transverse planes were negligible. Similar to Yang et al [3], we focused on quantifying gripping moments in the sagittal plane. From the SmartWheel, we obtained the moment generated about the hub (MHUB) and the forces parallel (Fx) and perpendicular (Fy) to the horizontal. Based on the previous studies, transformation from a global coordinate system (x,y,z) to a pushrim based r-t-n (radial, tangential, and normal) coordinate system (Figure1) was performed. To solve for Mgrip, moments generated by Fx and Fy must be computed which requires knowledge of the center of pressure or point of force application (PFA). An angle f was calculated between the horizontal and the PFA which was used in equations 1 to transform the forces. The tangential force was then multiplied by the radius of the pushrim, R, to obtain the propulsion moment, MPFA (equation 2). The gripping moment is the propulsion moment, MPFA subtracted from the moment measured directly from the SmartWheel (equation 3).
Equation 1 | FtPFA = Fx • sin Φ - Fy • cos Φ |
---|---|
Equation 2 | MPFA = FtPFA * R |
Equation 3 | MGRIP = MHUB - MPFA |
Only subjects who had at least three complete strokes in each trial on all surfaces were included in the analysis. The independent variables for the analysis were three surfaces: carpet, linoleum and ramp, and the stroke number: 1, 2 or 3. The dependent variables: peak hub moment, average hub moment, average velocity of propulsion, peak positive gripping moment, peak negative gripping moment and average of absolute moment for each of the three strokes was calculated. Data from the three trials on each surface were averaged together.
Statistical Analysis:
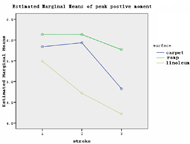
A two-way repeated measures analysis of variance (ANOVA) was used to determine the differences in gripping moments among three surfaces and three strokes. A Bonferroni adjustment was used if any significance was found. All statistical analyses were completed using SPSS software (SPSS Institute, Inc.) and α value was set at 0.05.
RESULTS:
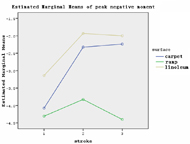
There were 23 subjects who met the criteria for the required number of strokes. There were 19 subjects with spinal cord injury, 12 of whom had thoracic injuries, four had lumbar injuries, and three had cervical injuries. One subject had a bilateral transtibial amputation, one subject had a unilateral transfemoral amputation, one subject had peripheral neuropathy, and another subject had spina bifida at L4. One subject with a lumbar SCI also reported having multiple sclerosis secondary to the SCI. Their mean age and years post injury or disability onset were 46.8+9.6, and 14.6+11.6 years respectively. Their average weight was 90.0+22.5 kilograms, and average height was 180.7+8.2 centimeters.
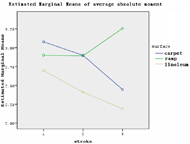
The average gripping moments (absolute value, no consideration of direction) were 2.81+1.47 (N*m), 3.02+1.18 (N*m) and 2.43+0.99 (N*m) which comprised 16.87 + 7.43 %, 20.17 + 12.65 % and 20.04 + 7.62 % of the average moments measured at the hub for carpet (16.02+4.35 N*m), ramp (17.47+4.93 N*m) and the linoleum (13.08+4.00) surface separately (Table 1). Both the ramp and carpet showed significantly higher peak grip positive moments compared to linoleum (Table 2). The ramp showed significantly higher peak negative moments compared to linoleum. Both ramp and carpet had significantly higher average absolute grip moment compared to linoleum (Table 1, 2). Profile plots of each variable for the three surfaces are shown in Figures 2-4
DISCUSSION:
Because CTS is so common among manual wheelchair users, quantifying the gripping moments during propulsion could provide further insight into the mechanisms that lead to CTS. Our results showed that the gripping moments were not as large as those reported in Veeger et al [1] however their study involved a small group of non-wheelchair users (N=5) and testing was conducted using a wheelchair ergometer. Our results were closer in agreement with Yang et al. [3] who found gripping moments comprised 11-14% of the measured propulsion moment for experienced wheelchair users with SCI. One reason why our gripping moments may be higher could be that we analyzed ‘start-up’ strokes whereas Yang et al. analyzed steady-state strokes. Forces and moments in general are usually higher during the acceleration phase of propulsion. Likewise, there may also be a greater need to generate gripping moments when starting propulsion from a rest position.
Our results indicate that more gripping moment was used on the ramp and carpet compared to the linoleum. Surfaces of higher resistance cause the wheelchair to decelerate more quickly in between strokes. This may require the user to exert more grip force and/or grab the pushrim differently since more propulsion force is also needed to keep the wheelchair moving forward on a difficult surface. Interestingly, the relative contribution of grip moment to the total moment measured at the hub was similar for linoleum and the ramp. This may be an indication that more grip moment is being used than is needed on linoleum thereby contributing to inefficiencies in propulsion technique and potentially elevating the risk of developing CTS.
In general more positive gripping moments were generated during propulsion over all surfaces. These grip forces add to the propulsive moment and therefore increase the mechanical effectiveness of the stroke [3]. Negative grip forces create a moment in the opposite direction of motion and therefore reduce the mechanical effectiveness of the stroke. Persons who have the inability to grasp the rim (e.g, individuals with low-levels of tetraplegia or others with limited hand function or grip) may be unable to generate positive grip moments. This may explain in part why manual wheelchair users with tetraplegia propel at slower velocities with less effective forces compared to persons with paraplegia [7]. Investigating the gripping moments on an individual basis may help to identify opportunities for intervention (e.g., use of an ergonomic handrim to enhance gripping ability) or to identify those who may be at greater risk for developing CTS due to poor propulsion technique.
CONCLUSION:
Gripping moments appear to play a significant role in wheelchair propulsion on natural surfaces. This study found that when faced with surfaces of higher rolling resistance, individuals exerted more gripping moment to propel at a desired pace. The relative contribution of gripping moments to the total moment measured at the hub was comparable between the linoleum and ramp surfaces which may be an indication that more grip force is being used on linoleum than is necessary thereby contributing to inefficiencies in propulsion technique and possibly increasing the risk of developing wrist pain or CTS, Investigating gripping moments on an individual basis may help to identify opportunities for intervention or to identify those who may be a greater risk for developing CTS due to poor propulsion technique.
REFERENCES:
- Veeger, H.E.J., Van der Woude, L.H.V., & Rozendal, R.H. (1991). Load on the upper extremity in manual wheelchair propulsion. Journal of Electromyography and Kinesiology, 1, 270-280.
- Vansickle, D.P, Cooper, R.A, Boninger, M.L, Robertson, R.N, & Shimada, S.D (1998). A unified method for calculating the center of pressure during wheelchair propulsion. Annals of Biomedical Engineering, 26, 328-336.
- Yang, Y.S., Koontz, A.M., Boninger, M.L., & Cooper, R.A. (2004). Influence of gripping moments on mechanical efficiency of wheelchair propulsion [CD-ROM]. Proceedings of the RESNA 27th Annual Conference; 2004 Jun 18–22; Orlando, FL. Arlington (VA): RESNA Press; 1995.
- Boninger, M.L., Impink, B.G., Cooper, R.A., Koontz, A.M. (2004). Relation between median and ulnar nerve function and wrist kinematics during wheelchair propulsion. Archiveof Physical Medicineand Rehabilitation; 85, 1141-1145.
- Asato, K.T, Cooper, R.A, Robertson, R.N, & Ster, J.F (1993). SMARTwheels: Development and testing of a system for measuring manual wheelchair propulsion dynamics. IEEE Transaction on Biomedical Engineering, 40, 1320-1324.
- Sabick, M.B., Zhao K.D., & An K.N. (2001). A comparison of methods to compute the point of force application in handrim wheelchair propulsion: A technical note. Journal of Rehabilitation Research and Development, 38, 57-68.
- Dallmeijer, A.J., van der Woude, L.H., Veeger, H.E., Veeger, H.E., Hollander, A.P. (1998). Effectiveness of force application in manual wheelchair propulsion in persons with spinal cord injuries. American Journal of Physical Medicine and Rehabilitation, 77: 213-221.
ACKNOWLEDGEMENT:
This work was supported by the VA Center of Excellence for Wheelchairs and Associated Rehabilitation Engineering B3142C and Paralyzed Veterans of America
AUTHOR CONTACT:
Hongwu Wang, Human Engineering Research Labs, VA Pittsburgh Healthcare System, Pittsburgh, PA 15216; Phone: (412) 365-4823, Fax: (412) 365-4858, Email:how11@pitt.edu.